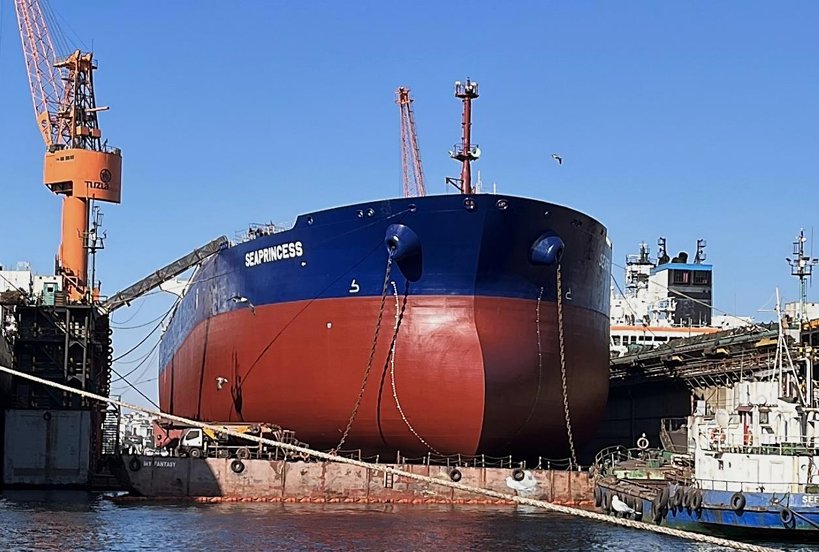
The Malta Transport Marine Safety Investigation Unit has released a report into a fatality on board oil tanker Seaprincess. The Maltese-registered ship entered TK Tuzla Shipyard, Türkiye, for its planned dry-docking on 29 July 2023. At the time of arrival in the dry-dock, all cargo and slop tanks had been washed, cleaned and dried, and declared gas free. The compartments were tested on a daily basis and while they had been declared to be gas free, they were only suitable for entry provided a personal gas monitor was worn. Moreover, the compartments’ environment was declared unsafe for hot work.
On 14 August, two welders from the repair riding team were told that they had to repair several stanchions in the port side slop tank. The damaged stanchions had been identified on 06 August, during a survey. After setting up the welding set and preparing the area, one of the welders, who had just started welding, noticed a ball of fire rising from the bottom of the slop tank, followed by a rush of air. He immediately shouted to his colleague to exit the slop tank and to head to the nearby vertical ladder. The force of the explosion ejected him to a height of about 12m in the air. A second explosion cushioned his fall on deck, as he descended.
The explosion caused a small fire inside the slop tank which, however, was immediately extinguished. After the slop tank was declared safe for entry, the body of the second welder was extracted from the slop tank.
Although the slop tank had been tested at 0800 and found to be gas free, the safety investigation concluded that in all probability, the cause of the explosion was the ignition of a small gas pocket that had built up at the lower levels of the tank and which must have escaped detection when the atmosphere was tested by the shipyard in the morning.
Conclusions
Findings and safety factors are not listed in any order of priority.
Immediate cause of the accident
- Welding splatters ignited undetected hydrocarbon vapour present inside the port side slop tank.
Conditions and other safety factors
- A quantity of oily-water mixture, which unknowingly had remained inside the decanting line between the two slop tanks, was released inside the port side slop tank.
- This oily-water mixture eventually released hydrocarbon vapour inside the tank.
- Ensuring that all interconnecting pipelines were flushed was a significant, daunting task and missing on interconnections comes as no surprise.
- The more the crew members, contractors and shipyard workers are engaged in the numerous, simultaneous tasks which need to be carried out whilst the vessel is in the shipyard, the more complex the situation becomes.
- Although the slop tank had been tested at 0800 and was found to be gas free, the safety investigation concluded that the build-up of a small gas pocket at the lower levels of the tank escaped detection when the atmosphere was tested by the shipyard that morning.
- It was possible that the two welders were either unaware that the slop tank was not cleared for hot work, or they had missed the warning sign altogether.
- Although the vessel’s procedures required all interconnecting pipelines between compartments to be flushed through and vented, this did not occur.
- The safety investigation identified instances where communication may have been an issue. The OOW, senior officers and the superintendents were all unaware that entry into the port slop tank and hot work was being contemplated that morning by the riding team.
- Considering the timing of the completion of the safety round checklist, even if the duty officer conducted his safety round in accordance with the checklist, he would have been unaware of the work that was about to take place at around 0900 – unless he was told about it, or he happened to be in the vicinity of the entrance.
- The two welders had no cues that a simple welding task would have led to tragic consequences.
- Whilst the safety investigation did not exclude that the two repair team members may have been aware of the oily-mixture leak inside the slope tank, the risk related to such a leak was either not identified, or not appreciated by them.
- Recollections of all those present indicated that this incident had not been reported because the presence of the oily-mixture only became known after the explosion happened.
- The safety investigation believes that the entry into the enclosed space, and the eventual commencement of the hot work, was a situational performance variability, ‘instigated’ and consequential of the prevailing complex, operational context, which one would typically find in a shipyard.
Other findings
- Fatigue and alcohol were not considered to be contributory factors to this accident.
Recommendations
In view of the conclusions reached and taking into consideration the safety actions taken during the course of the safety investigation, the Company is recommended to:
- 11/2024_R1 Circulate the findings of this investigation to all vessels under its management.
- 11/2024_R2 Analyse how communication gaps in shipyards, among crew members and other personnel on board Company ships can be bridged, taking into consideration the expected prevailing context on board a vessel in a shipyard.
Read the full report: MT-Seaprincess Final Safety Investigation Report