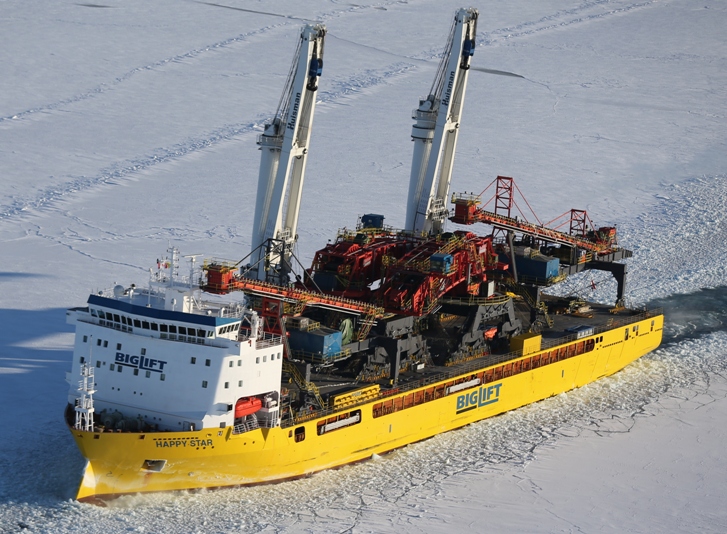
By Capt Andrew (Drew) Frank Korek, MIIMS
Whilst many of us were enjoying the Christmas period in the comfort of our own homes, for one IIMS member and marine surveyor it was a Christmas with a difference. This is Drew Korek’s story and account about the ‘heavy lift’ loading of the Happy Star using extracts taken from his report with his permission.
As The Report magazine went to press, Drew had just completed overseeing the load off the ship in Quebec. The whole project has captured the attention of the media too. This fall you will be able to watch a conclusion of this captivating project and portion of the Happy Star voyage from China on Discovery Channel show entitled Mighty Ship’s.
During this project in China and then Canada Drew has been a willing and regular correspondent keeping the IIMS head office team up to speed with daily photos and anecdotes. Often operating in Canadian temperatures of minus 30 Celsius (and lower), Drew found his IIMS work wear essential to keep him warm and visible at all times. The last we heard, Drew was heading for a very well earned rest.
Background to and scale of the project
Sandvik Canada Inc. chartered a heavy lift vessel Happy Star from the BigLift Shipping BV to transport two complete shiploaders from Guangzhou, China to Quebec, Canada. Cargo operations were carried out at GSI Shipyard at Longxue Island. Ships cranes were utilized for loading and shifting of the cargo on board. Shore mobile cranes, trucks and SPMTs were used to move cargo from storage areas to the loading berth and to provide peripheral assistance during loads rigging, placement and items alignment. GSI Shipyard personnel handled cargo moves on shore with assistance of Vastwin SPMTs operator. Cargo rigging for lifting with the ship’s cranes on shore side was carried out by GSI riggers working under the guidance and close supervision of the BigLift personnel. All cargo and load handling on board the vessel was carried out by ship’s crew under supervision of the BigLift’s load master.
https://www.youtube.com/watch?v=IOVSLxuji54
Drew was appointed as Marine Warranty Surveyor by Liberty Insurance Underwriters and Sandvik Mining & Construction of Canada to attended vessel Happy Star whilst she lay afloat alongside at GSI Shipyard, Longxue Island, Guangzhou, China from 18th to 29th of December 2014 to ensure that loading operations were executed in a safe manner and according to the standards required and customary to such operations including compliance with the applicable lashing, rigging and cargo securing rules of Det Norske Veritas (DNV). Furthermore to observe and assure that cargo operations were carried out with care, utilizing generally accepted stevedoring practices.
Heavy Lift cargo consisted of two (2) complete shiploaders and wharf conveyor comprising:
1. Shiploader 1 (SL01) 970 MT
2. Shiploader 2 (SL02) 970 MT
3. Tripper Car 1 (TC01)
4. Elevator Car / Tripper Car 2 (TC02)
5. Tripper Tail 1 (TT01)
6. Tripper Tail 2 (TT02)
7. 28 Conveyor Galleries, partly stacked
Plus an additional 73 pieces of peripheral equipment associated with this complex machinery.
Cargo weight in total: 3,047,721,24 kgs (gross weight)
About BigLift Shipping
BigLift Shipping is one of the world’s leading heavy lift shipping companies, specialising in worldwide ocean transportation of heavy lift and project cargoes with a history going back to 1973. BigLift Shipping strives for innovation, excellence and operational reliability, adhering to high standards of health, safety, environment and quality, operating to strict time schedules.
BigLift Shipping comprises a team of dedicated, highly skilled professionals with years of experience and the mindset to think creatively. They careful planning, engineering, coordination and supervision skills to ensure that safe transportation is all in a day’s work.
In 2013 and 2014 the vessels of the Happy S-type entered the BigLift fleet. These flag ships have a lifting capacity of two times 900 mt, combinable to 1800 mt. The length of the vessels and the forward position of the superstructure offer a single large cargo hold and a wide open deck area. The vessels have the notation for open sailing, allowing for more flexibility for large and high cargoes.
The vessels also have the highest Finnish Ice class notation. A key factor in the safe and reliable operation of these super heavy lifters is to perform cargo operations without using any stability pontoons during lifting operations. Following questions from the market, both vessels’ cranes were extended to provide more lifting height and more outreach, thus offering superior lifting capabilities. The cranes on both vessels are prepared to have the flyjib mounted, extending lifting height and outreach even further.
About Happy Star
During the design phase it was decided to adapt the design of the Happy Star to answer the direct needs of the market. So, the crane pedestal is raised by 4 metres and the jib is extended by 6 metres, providing 10 metres more lifting height and 6 metres more outreach. This gives the vessel a crane curve which is unmatched amongst heavy lift vessels and allows cargoes to be lifted higher and further away than in the vessel’s original design.
As a direct consequence, the beam of the vessel is increased to 29 metres. This provides the vessel with sufficient anti-heel capacity and stability to use the cranes to their full capacity, being 1800 mt at 25 metres metres, 1600 mt at 28 metres and 1000 mt at 41 metres with a lifting height of close to 47 metres above the main deck. The stability is achieved without the need for a stability pontoon during loading or discharging operations.
To provide a maximum useable deck area, the weather deck extends over the full width of the vessel. It has 8 pontoon type hatch covers, with a 15 t/m2 carrying capacity over the full length and beam. The tweendeck adjustable in height and it is possible to sail with open weather deck hatches on a draft of up to 8 metres. The hull was adapted to the new dimensions and, using modern design methods, special attention was given to optimizing the powering performance, resulting in a speed of 17 kn.
Drew said about the project, “To the Happy Star crew for this bohemian task of superb handling and securing those monstrosities I salute you.“
“The sheer amount of lashing applied to the deck cargo which can be seen on some of the photographs included in my report. Those lads worked very hard to accomplish the text book result and should be commended.“
“My kudos goes to SPMT Vastwin personnel for superb, flawless handling of those giants in safe and timely fashion.”
“And of course my highest commendation to GSI shipyard personnel for attending to every imaginable task on hand – and there were many!”
On a different note, Drew commented, “I have to admit I was admirably shocked seeing 15,000 GSI employees crossing the shipyard’s gate every morning and accomplishing unimaginable results in ship building.”
“I have never before seen over 20 vessels growing before my eyes in the matter of few weeks.”
As a conclusion, Drew was keen to give huge credit to BigLift Shipping for the intricate planning that ensured the success of this enormous undertaking and project.