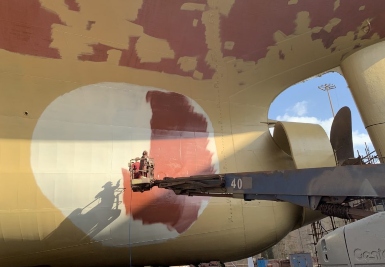
Corrosion has emerged as the arch-enemy of the exhaust gas cleaning systems as the uptake of the technology rose with the entrance into force of the IMO 2020 sulphur cap.
Like with any new technology, scrubber maintenance and operation has been a learning curve for ship owners and operators, especially in the context of preventing failures of the technology and reducing downtime.
“Corrosion mainly happens on the overboard pipes, the last piece from GRE piping and connection to shell plating of the hull, especially near the connections and welding seams, and the area on the external hull around the overboard pipe outlet,” said Manuel Hof, Sales & Production Executive, NACE Coating Inspector Level 2 at Subsea Industries.
“These areas will need to be protected against acid-containing water (highly corrosive sulphuric acid) coming from the exhaust gas cleaning system. Traditional coatings applied inside the overboard pipes and on scrubber outlet areas are in most cases not chemically resistant. In that case, the coating will degrade, the steel will be affected and corrode. This can result in water ingress in the engine room, ballast tanks and cargo holds.”
“Scrubbers that are scheduled to be installed will still need to be completed. Now we see quite a lot of issues from scrubbers installed last year with corrosion and leakage problems. Protection systems are failing after a few months in service. We have been involved in repairs where it was required to replace overboard pipes of the vessel while still in the water,” he added.
As explained, the lower the pH value of the discharge water after cleaning, the more acidic the fluid and higher likelihood of corrosion.
“Material selection is also important. That is why scrubbers are made of special materials and most of the piping made of GRE/GRP. The last part of the overboard pipe and area of the hull will be in steel. Protection on those areas is very important, if not vital. To apply the correct coating system is essential and should not be tampered with,” he added.
Hence, coatings for scrubbers have become as equally important as good quality material of scrubber components.
Read another article about the IMO Sulphur Cap here: IMO sulphur cap: Joint industry guidance for the supply and use of 0.50% sulphur fuel published