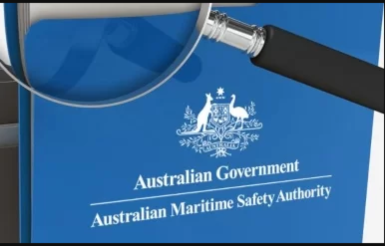
The Australian Maritime Safety Authority (AMSA) has published a safety alert to draw the attention of vessel operators to the importance of planned maintenance in ensuring the safe operation of domestic commercial vessels in Australia.
Planned maintenance is essential on domestic commercial vessels. Good maintenance work in port or at anchor can help avoid breakdowns and getting into hazardous situations at sea. Recent incidents have demonstrated the potentially serious consequences of a lack of effective maintenance that can pose serious risks to the safe operation of vessels. Analysis of 117 incident investigations since 2020 found that maintenance problems were a factor in 28% of incidents, including half of the very serious incidents and 27% of serious incidents.
Plan maintenance to suit the vessel, the type of operation and potential risks
There is a wide range of domestic commercial vessels and types of vessel operations. In many cases, breakdowns and equipment failure can present significant risks. Factors that can increase the consequences of breakdown could include:
– lengthy voyages from port;
– operation in deep water where anchoring is not possible;
– weather conditions and potential for change;
– operation in remote areas where parts and assistance are not available;
– operation in high traffic areas where anchoring or drifting may be dangerous.
As well as a safety risk, breakdown and equipment failures can present serious economic and reputational risks to businesses. This is particularly so for passenger vessels and hire-and-drive operations.
Heed manufacturers’ recommendations
Most engines and equipment have documented recommendations on maintenance schedules and requirements. These should be used to guide the development of planned maintenance schedules documented in each vessel’s safety management system (SMS). Maintenance schedules can also be built around seasonality in the vessel’s operations. For example, commercial fishing closures and times outside tourist season can provide ideal times for major maintenance.
AMSA recognises that several factors presented challenges to effective maintenance during the COVID-19 pandemic restrictions. These included supply chain difficulties in getting necessary parts and specialist expertise to affected vessels and shutdowns of some operations such as tourism and some commercial fishing. However, with travel restrictions and quarantine requirements now largely removed in Australia, AMSA expects operators to have resumed effective maintenance action.
Safety gear checks
A key component in any planned maintenance schedule is periodic checking of safety gear. Life jackets and life rafts should be checked for wear and tear. Monitoring the expiry dates of safety equipment and some first aid kit items is essential. These can either be checked regularly or by building expiry date alerts into electronic or paper calendars or diaries.
Legal requirements
Under the National Law for Domestic Commercial Vessels, Marine Order 504 explains the requirements for safety management systems (SMS). It sets out that:
– The owner of a vessel must ensure that a system of regular programmed inspection and maintenance appropriate for the vessel, its machinery and its equipment is developed, maintained and implemented.
– The SMS must include arrangements for recording details of each inspection and correcting each deficiency identified by an inspection. The record may be kept in the logbook.
– The vessel must be inspected sufficiently to determine if the vessel, its machinery and its equipment comply with the maintenance and operation requirements that apply to it. This requirement does not prevent inspections being made for compliance with voluntary maintenance guidelines.
– The vessel must be serviced taking into account the manufacturer’s specifications and requirements.
Under Marine Order 503, it is a condition of a Certificate of Survey that a certificate of currency relating to equipment that is required to be carried on the vessel must be kept current.