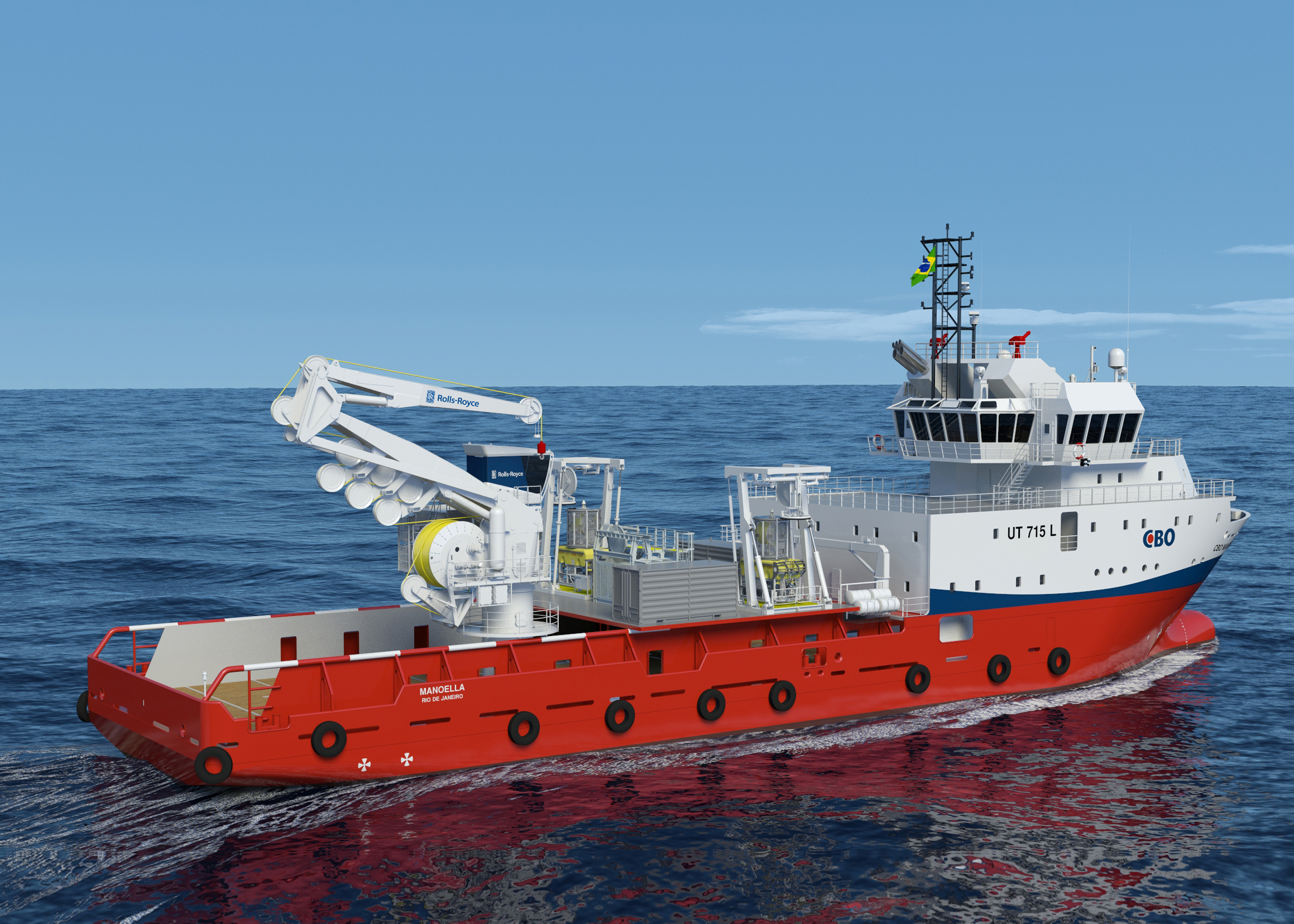
A refit that’s turning a PSV into a ROV support vessel is taking advantage of a very new subsea crane that can handle both wire and fibre, providing flexibility in a challenging market.
The 76.7m platform support vessel CBO Manoella is one of a pair that’s being transformed into RSVs. As a Rolls-Royce UT715 design that first went into service in 2009, this vessel isn’t exactly old: however the market has changed dramatically during its lifetime. Despite that, this series of ‘North Sea standard’ PSVs were designed to be practical, flexible workhorses with a fair sized deck and good sea keeping characteristics, so it’s no surprise that Manoella’s adaptability has found it work in other segments.
On the RSV’s deck will be one of Rolls-Royce’s new generation of dual draglink, active heave compensation (AHC) subsea cranes: most importantly, this will be the first installation of a subsea crane designed to be able to use either fibre or steel wire rope. The crane will have an operating depth of up to 3,000m, able to lift 50 tonnes at 11.5m, or 23 tonnes at 20m outreach. While it will be equipped with wire rope when it embarks on its first subsea assignment off the coast of Brazil, it can swap the steel for low weight fibre rope – increasing the effective lift capacity at some of the more extreme depths.
It’s fruit of some fairly intensive R&D: the big issue for fibre development has been dealing with the small, but not insignificant lengthening that this kind of rope displays when it heats up, typically from cycling regularly over an AHC unit. To counter this, Rolls-Royce has put a cooling system in place and given the main winch a further agenda, developing it into a cable traction control unit (CTCU) that can keep a constant tension on the rope.
The particular variety of crane also helps to mitigate the friction: this dual draglink unit doesn’t place all the AHC stress on the winch, but instead compensates by controlling the position of the derrick’s elbow hydraulically. As a result, the amount of time the winch spends cycling is minimised, reducing wear – and heat build up – on the cable itself.
There are other benefits: one of them is that since the CTCU is tucked away near the main boom, it doesn’t need placing under the deck, making retrofitting easier. Further, fibre’s low weight means that the vessel’s deck load capacity can be increased by approximately 100 tonnes.
Flexibility is the name of the game as CBO’s technical director Marcelo Martins pointed out: “A hybrid solution, with use of either fibre or wire, makes the vessel better prepared to take on a larger variety of future subsea tasks.”