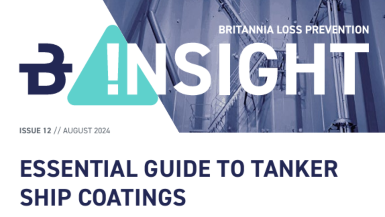
According to Britannia P&I Club, who have produced this essential guide to tanker ship coatings, tanker ships rely on specialized coatings for their onboard tanks to safeguard against corrosion and contamination.
The Club has published a guidance tanker ship coatings which explores the different types of coatings, including stainless steel and pure epoxy, giving details of their properties, advantages, and limitations.
A reliable and effective tank coating prevents water and corrosive agents from coming into direct contact with the metal surfaces, reducing the likelihood of structural damage and preventing cargo contamination during transportation. Therefore, it is essential to understand the significance of tank coatings and how they can impact claims and risk management.
Types of tanker ship coatings
Several types of cargo tank coatings are available, each with their own properties and advantages for various product types.
Stainless Steel
Stainless steel is technically not a coating. However, it is a common tank lining found on the majority of chemical tankers. Commonly used alloys in the tanker industry include: 316 and Duplex stainless steel. The 316L or LN-graded alloys are predominantly used where the surfaces in between cargo tanks are made of solid stainless steel and the surfaces between cargo tanks and adjacent ballast tanks or void spaces are cladded.
“Cladded” implies a three-millimetre stainless steel layer has been applied to the construction steel of the vessel. One distinctive property of stainless steel is the presence of a chromium-oxide layer, often known as the “passive layer”. This ultra-thin layer, measuring about three-nanometers in thickness, serves as a protective barrier between the stainless steel and the product carried in the tank. This passive layer may deteriorate over time when exposed to specific cargoes. Nevertheless, stainless steel has the natural capability to regenerate this passive layer when it interacts with oxygen. The integrity of the chromium-oxide layer is commonly referred to as “passivity”. To facilitate the complete restoration of the chromium-oxide layer in stainless steel, it is recommended that stainless steel cargo tanks are exposed to air for a duration of 24 to 72 hours after tank cleaning. However, this may not always be achievable due to quick turnarounds where discharging, tank cleaning and loading are carried out consecutively.
Best practice: It is recommended to conduct a thorough inspection of the cargo tanks after each cleaning operation, not only for cleanliness, but also for a visual assessment of the steel’s surface condition. Depending on the trade activities, the passivity of the steel should be measured periodically. During these inspections special attention should be paid to the condition of stainless steel heating coils. Often, the presence of pitting can lead to the development of pinholes. Pinholes can result in cargo contamination by the heating medium – typically water (occasionally mixed with glycols) or thermal oil. To ensure the integrity of these coils, a regimen of pressure testing should be established before their utilisation, complementing the standard visual examination.
Additionally, special care should be taken prior, during and after the carriage of acid cargoes because they have the potential to form aggressive mixtures which react chemically with the stainless steel, causing corrosion damage. Depending on the severity of such damage, repairs may turn into costly affairs on account of labour, materials and operational delays.
Pure Epoxy – Organic Coating
This coating is Typically used for vessels in the clean petroleum products (CPP) trade, pure epoxy has a low resistance and therefore limited flexibility among cargo types. Poor corrective maintenance and failure to clean tanks properly after transporting cargoes can lead to the accumulation of particulate matter or retention of cargo and/or cleaning water residues, causing subsequent cargoes to be contaminated. When subjected to improper cleaning methods or exposure to elevated temperatures, epoxy coatings may degrade faster, making them susceptible to accelerated deterioration and transforming them into potential sources of cargo contamination. The binder within organic coatings can be chemically attacked by unsuitable or incompatible cargoes, such as palm fatty acid distillate and other vegetable acid oils in a pure epoxy-coated cargo tank. The cargo resistance list should always be consulted.
Best practice: Owing to the nature of trade, cargo tanks often undergo minimal cleaning or, at best, a freshwater bottom flush between cargoes. If an extended tank clean is required, then special attention should be given to the cleaning agent used and the temperature of the cleaning water. Certain cleaning agents are very effective in removing previous cargo residues but can be harmful to the epoxy coating too.
A routine inspection should be in place to periodically assess the condition of the coating. Localised coating breakdown may expand rapidly and should be addressed as soon as possible. Failure to do so may result in particulate matter contamination (coating flakes or rust particulates) or even cargo/moisture contamination. When the coating has softened, sufficient time should be granted for the coating to harden. Exposure to additional heat should be avoided to prevent the top layer of the coating hardening, while the underlying layers remain soft. Manufacturers’ guidance should be followed in terms of cargo compatibility as well as exposure to heat and cleaning agents.
Conclusion
Overall, tanker ship coatings systems demand vigilant monitoring over time and are not to be neglected after application. The demanding environment and harsh conditions to which coatings are subjected to require a continuous and thorough monitoring regime to detect any issues at an early stage. Owners and crews should have a clear understanding of the practical properties and constraints or limitations of the coating system applied. By treating the coating system with care, the risk for coating-related cargo contaminations and associated claims can be minimised. Furthermore, such attentive care contributes to extending the lifespan of the coating system and will therefore be cost effective.
Download the guidance: Tanker Ship Coatings