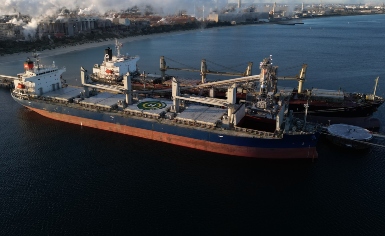
Britannia P&I Club warns against the risks of cargo fumigation and presents steps people onboard can take in order to mitigate those risks.
Fumigation is an effective approach to eradicate living organisms, such as insects or rodents, and is used to mitigate the transmission of invasive species or phytosanitary risks when transporting an agricultural cargo from one port to another.
Cargo fumigation risks
Both methyl bromide and aluminum phosphide, chemicals used for fumigation, are toxic to humans and to the intended targets of insects and rodents, Britannia warns.
Unfortunately, by the time fumigant gas is detected, it is sometimes too late to prevent poisoning, since the concentration of gas may be above the safe working limit.
When phosphine gas, without the presence of any impurities, is released, it is colourless and odourless. However, when contaminants exist, phosphine gas may give off white-coloured smoke and/or the smell of decaying fish, garlic or carbide. Methyl bromide is colourless but comes with a fruity or musty odour at high concentrations, Britannia adds.
These odours serve as good warning signs of gas leakage to people working in or near the cargo spaces. However, these indicators should never be solely relied upon as a means of determining whether a space is safe.
Below are some of the practical preventive measures recommended by Britannia P&I Club that should be undertaken during or before the voyage:
– Before reaching the loading port, maintenance should be carried out on the weathertight integrity of the cargo hold, such as hatch cover seals, hatch cleats, ventilators, cement ports and booby hatches. It is recommended that, as the hatch covers and other access points have to be gas tight to ensure their integrity. Prior to arrival, any necessary repairs should be conducted in good time and their effectiveness verified.
– Records of inspection and maintenance should be kept on board for a suitable period prior to fumigation.
– The fumigator should conduct inspections of all access points to the cargo holds to ensure they are suitably gas-tight for the fumigation process. This should be done when the hold is empty and in accordance with the requirements in the countries of loading and discharging. The master should sign off the pre-fumigation inspection report.
– The fumigator should ensure the formulation of fumigant is used at the correct dosage and is applied evenly to the cargo surface/subsurface. The application areas should be free from excessive moisture.
– To avoid fires it should be ensured that tablets and pellets on surfaces cannot roll and be collected at the hold plating.
– The master and ship’s crew should carry out a thorough onboard search to confirm there are no stowaways or unauthorised personnel in the cargo spaces. All of the ship’s crew should be accounted for before starting fumigation.
– The master and crew should also familiarise themselves with the fumigation procedures and precautions required when working near fumigated cargo areas and be aware of any warning notices posted at the entrances to holds on deck.
– The master may appoint at least two crew members to maintain safe conditions in the fumigated spaces on board, including testing the atmosphere. These crew members should be trained to use the gas detecting equipment.
– Upon completion of the fumigation process in each hold, all access points should be padlocked and ideally sealed with a customs seal or similar (and the seal number recorded). This means it should be easily seen if an access hatch has been opened. Keys for padlocks should be carefully secured by the chief officer.
– The treatment or exposure period for fumigation at sea, and in particular when the cargo spaces should remain sealed, should be made clear in writing to the ship’s crew by the fumigator.
– Aeration and ventilation after the exposure period should be performed according to the guidelines specified by the fumigator.
– When determining the period required to ventilate the cargo holds, a number of factors should be considered including type of fumigants used, method and rate of fumigant application, voyage duration, weather and temperature conditions, likely risks of gas desorption, and gas readings.
– It should be ensured that the aeration and ventilation processes do not result in the fumigant gases being blown into air duct intakes for enclosed accommodation spaces, the engine room, deck lockers or routine working spaces.
– The master should ensure regular checks are carried out at the specified intervals recommended by the fumigator to detect gas leakage within spaces occupied by crew, or whenever and wherever there is any suspicion that fumigant gas may be present. This is particularly the case when crew members shows signs of feeling uncomfortable. This should not be taken lightly and mistaken for motion sickness at sea. If there is any doubt, the atmosphere should be tested.
– In the event that the ship’s crew shows any signs of poisoning, the master should take immediate action to evacuate crew from the affected spaces whilst using PPE.
– Gas detection equipment suitable for the intended fumigant should be provided, such as tube gas test equipment, photo-ionisation gas testing and monitoring equipment with the correct sensors.
– Proper protective respiratory breathing equipment (a minimum of four sets is recommended) should be provided for the vessel prior to starting the voyage.
– Disposal of the sleeves/residue should be performed by the approved fumigator’s representatives in accordance with local and international regulations, with the use of appropriate PPE.
– After gas freeing and removal of residues, the fumigator’s representatives should test the environment inside the cargo spaces with the gas detection equipment to confirm fumigant concentrations are below the threshold limit value (TLV). The ship’s crew should verify that the gas-free testing is physically carried out up to the recommended maximum allowable PPM concentration as per the fumigator’s instructions.
– A gas-free certificate for the vessel can only be issued by the fumigator in-charge when the cargo spaces are tested to show all residual fumigant has been dispersed from the cargo spaces and adjacent working spaces, the residual fumigant materials removed, and found safe for entry.
Download the overview: Loss Prevention Insight