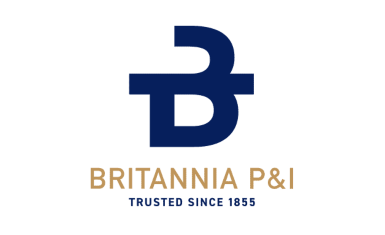
Britannia P&I club has released guidance highlighting the importance of understanding the intricacies of mono ethylene glycol (MEG) and some of the safety considerations for its transportation.
MEG CARGO OVERVIEW
For reference and as background to understanding the cargo, it’s important to know that MEG is a high specification and particularly sensitive cargo. MEG is a chemically hydrophilic substance, meaning it can easily form hydrogen bonds with solvents such as water or alcohol, it also has a low freezing point. Typically, it is synthesised by reacting ethylene oxide with water and the product is practically colourless, odourless and sweet tasting with a syrupy appearance.
Therefore, the production process poses a unique challenge due to the formation of impurities such as aldehydes (by-products), which are inherently difficult to separate from MEG. Factors like production process instability or failure in process control can contribute to the presence of aldehydes, specifically formaldehyde or acetaldehyde, in MEG.
LOSS PREVENTION
Often, claims arise from contamination due to previous cargo residue, degradation due to oxygenated impurities, and/or moisture content. Vigilant adherence to safety protocols and thorough understanding of MEG’s unique characteristics are imperative to minimise the risk of such claims during maritime operations.
Below are some practical considerations and recommendations when dealing with MEG cargoes:
Pre-loading
• Ensuring proper tank cleaning, including rinsing with fresh water after sea water washes, is essential for eliminating chloride-containing residues. In specific circumstances when the cargo grade demands 99% purity, it is advisable to consult with the shipper/ charterer regarding the necessity of the final wash cycle (heated) with de-mineralised water prior commencement of the voyage
• Conducting thorough pre-loading surveys of the cargo tanks, pumps, heating equipment, fixed tank cleaning machines, and cargo/ vapour lines is a necessary step
• Prior to the initial cargo quality sampling, perform a visual inspection of the tanks and conduct wall-wash tests thereafter to determine if the tank is clean enough for MEG cargo. If required, prior to loading conduct a test for the presence of chloride in the tanks
• Ensure proper drainage of washwater from the lines to prevent undesirable moisture from being trapped and migrating into the cargo tanks
• Cargo tanks should always be mopped and dried thoroughly to limit any increase in water content during loading
• Obtain a certificate of cleanliness before loading to ensure the cargo tanks are dry and free from remnants of previous cargo residues and/or washwater
• Cargo tanks should preferably be nitrogen purged prior to loading in order to remove moisture
• The first-foot sampling provides valuable insights into the cleanliness of the cargo tanks and lines and the moisture content increase in the first foot sample may be expected so endeavour to avoid sampling repeatedly in a humid environment
• Promptly address any identified contaminants
• Be aware of cargo tanks equipped with epoxy-type lining systems that can potentially absorb light solvent species, such as aromatics
• For each set of samples that the cargo surveyors takes, one set should remain on board for the ship owners
• All the sample bottles should preferably be amber coloured glass bottles as MEG is very sensitive to sunlight
• All the samples should be taken to the maximum level of the sample bottle. This is in order to avoid air/oxygen being retained in the empty space
• All the sample bottles should be purged with nitrogen prior to the sampling as MEG is sensitive to oxygen
• Always use clean and appropriate sampling equipment (preferably closed sampling equipment)
• Always flush the sampling point prior to drawing a sample
• Issue a LOP to shippers/charterers if they do not arrange for nitrogen padding/blanketing.
During transportation
• MEG is a hygroscopic cargo, meaning it will readily absorb water from the atmosphere during transportation
• Check to ensure there are no leakage from the pressure-vacuum (p/v) valves for each tank and the targeted tank pressure is maintained to prevent ingress of moisture
• Certain cargoes demand close control of temperature, or control headspace atmosphere, by either total exclusion of oxygen or partial reduction for oxygen to a prescribed range
• Shippers and/or charterers should also provide their instructions with regards to the cargo care and the use of nitrogen padding for a long sea passage
• A ship without nitrogen generator should have sufficient replenishment of nitrogen gas supply or compressed nitrogen bottles for topping up in later part of the voyage, if required
• Avoid unnecessary internal tank transfer of cargo after loading and reducing the transhipments between loading and receiving end to a minimum may help to avoid cargo contamination
• Keep a record of the nitrogen gas log for each tank(s) headspace during the voyage, starting from the completion of the nitrogen padding/blanketing until the ship reaches the destination port before discharging, to preliminarily rule out any improper handling of the cargo during transportation.
Safety tips
• Avoid carrying incompatible products consecutively in the same cargo tanks
• Cargo tanks should be thoroughly cleaned after shipment
• Take shore tank samples and samples from cargo tanks during loading operation at regular intervals
• Take samples from the ship’s tanks during discharge for safe keeping
• Preserve the samples taken and store in a cool, dark place which is out of direct sunlight to avoid deterioration. The samples may serve as future evidence of the quality of the cargo.
Crew members’ experience becomes crucial when it comes to handling such a sensitive cargo. Therefore, aside from the above considerations, conducting thorough risk assessments and providing comprehensive training are fundamental steps to identify any potential hazards and ensuring safe and efficient operations. It is important to also brief the team extensively on the cargo’s properties, on correct sampling procedures and equipment usage before loading.
The guidance released by Britannia also looks into the quality of MEG cargo vulnerabilities, examples of MEG grades and technical considerations.
Download the full PDF: Safe Handling of Mono Ethylene Glycol (MEG) Cargoes