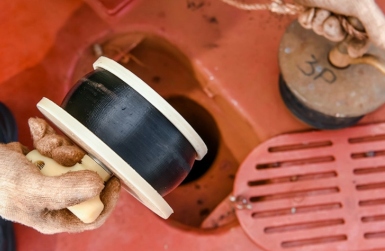
Berge Mafadi, a 300,000 dwt bulk carrier operated by Berge Bulk, has received the world’s first commercial delivery of 3D-printed scupper plugs. Berge Bulk is one of several companies enrolled in a Wilhelmsen Ships Service early adopter program that gives customers access to on-demand additive manufacturing. Other customers for the program, launched in December 2019, include Carnival Maritime, Thome Ship Management, OSM Maritime Group, Executive Ship Management and Wilhelmsen Ship Management.
“We are very excited with this milestone — completing one of the first commercial deliveries of 3D-printed parts in the maritime industry,” says Hakon Ellekjaer, Head of Venture, 3D Printing, Wilhelmsen Ships Service. “This is just the beginning of the journey, and we are quickly expanding our offering, together with our key development partners, enabling our customers to benefit from the savings provided by 3D printing, digital inventory and on-demand localized manufacturing.”
Parts in this program are being monitored in close collaboration with class society DNV GL. Through a unique selection, digitization, and documentation process, every part goes through a quality-controlled process whereby each is given a print passport number. All necessary documentation relating to the manufacturing, design, and performance requirements of each part is then captured and enclosed with the delivered part.
DNV GL, through the Print Passport Number and its published rules and standards, is providing system wide assurance to the Wilhelmsen 3D Printing venture.
“Wilhelmsen, Ivaldi, and DNV GL are testing a new universal part tracking system for purposes of quality control, part evolution and traceability of parts. The first 3D-printed scupper plugs have been given unique identifying codes and are logged in a trial system that should enable tracking throughout the lifetime of the part,” says Simon Ratcliffe, DNV GL.
Wilhelmsen and Ivaldi have delivered several 3D-printed parts to the Berge Bulk vessel, and scupper plugs were one of the part categories.
There are numerous scupper plugs on a vessel. For convenience and readiness, each drainage hole on the open deck has its own scupper plug. Scupper plugs are used for closing drainage holes to prevent oil spills or other contaminant spills on a ship.
“Scupper plugs are expensive, and there are no universal dimensions, which means that when you have a broken element, you have to buy a new scupper plug. With additive manufacturing, we are able to procure scupper plugs faster, cheaper and locally. If any part breaks, we can replace that one part instead of the whole unit. We are excited to be part of the Early Adopter Program. On-demand additive manufacturing will revolutionize the spare parts industry” says Sim Teck Siang, Procurement Manager, Berge Bulk.
The 3D-printed scupper plugs are equally as functional as traditional versions. In addition, they are an assembly, which means that if a part breaks, that one part can easily be replaced, instead of the whole scupper plug. Making them available through a digital warehousing solution means they are faster and easier to procure worldwide. It also means, thanks to on-demand manufacturing technologies, that only the exact number of parts required are produced, reducing costs and environmental footprint.