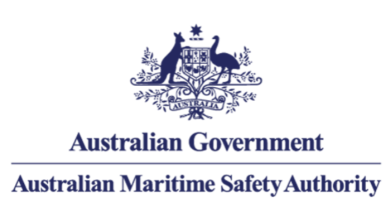
In an effort to enforce strict environmental standards, the Australian Maritime Safety Authority (AMSA) has outlined detailed guidelines for the installation and testing of oil filtering equipment, specifically oily water separators, on ships.
In particular, oil filtering equipment installed on a ship on or after 1 January 2005 must be approved to meet Resolution MEPC.107(49) to comply with MARPOL Annex I Regulation 14.
The requirements include:
– a truly representative sample of the effluent with adequate pressure and flow is supplied to the 15ppm bilge alarm;
– provision of fail-safe arrangements to avoid any discharge in case of malfunction of the 15ppm bilge alarm;
– 15ppm bilge alarm is fitted with an electronic device that is pre-set to activate when the effluent exceeds 15ppm and operates automatically if at any time the 15ppm bilge alarm should fail to function;
– the response time of the 15ppm bilge alarm. This is the time that elapses between an alteration in the sample being supplied to the 15ppm bilge alarm and the ppm display showing the correct response. Response time should not exceed 5 seconds;
– the setup of the installation must minimise the time it takes for the system to respond when the discharge from the 15ppm bilge separator exceeds 15ppm. This includes the time it takes for the automatic stopping device to activate and prevent discharge into the water. This should take less than 20 seconds. It must not exceed that limit under any circumstances.
AMSA Port State Control procedure
AMSA Port State Control officers (PSCOs) will inspect the condition, and operation, of the oilywater separator, filtering equipment and alarm, stopping or monitoring arrangements as described in the Procedures for Port State Control, 2023 Resolution A.1185(33). Operational testing of oil filtering equipment will require the equipment to be configured to circulate liquid from bilge tank to bilge tank (recirculating facility) and provide an effluent sample to the 15ppm bilge alarm – simulating the discharge of 15ppm bilge separator effluent overboard. When a simulation of effluent sample greater than 15ppm is applied, the PSCO will confirm that the alarm is activated, and that the automatic stopping device (3-way valve) stops effluent discharge overboard. This indicates compliant operation of the system. The PSCO will confirm that there is a flow of effluent sample from the 15ppm bilge separator that is truly representative, with adequate pressure and flow, to the 15ppm bilge alarm while effluent is being simulated to flow overboard.
In cases where the flow of effluent sample is not a representative sample, including blockage of the sample line or incorrect operation of valves, it is expected that, in accordance with MEPC.107(49) requirements, the fail-safe arrangement will activate the automatic stopping device (3-way valve) and stop effluent discharge overboard. AMSA’s interpretation is that the failure of the 15ppm bilge alarm to activate the automatic stopping device in the absence of a representative sample of the effluent, represents noncompliance with Resolution MEPC.107(49). That is there is no fail-safe arrangement required by technical specification 4.1.3.
AMSA is aware various classification societies advocate for the installation of “flow sensors” in the 15ppm bilge alarm sample line. The flow sensors activate an alarm and operate the automatic stopping arrangements when a truly representative sample, with adequate pressure and flow, is not present at the 15ppm bilge alarm. They also recommend the sealing of all valves installed in the effluent sample pipes so that the valves are locked and sealed in their normal operating position to ensure adequate effluent sampling. AMSA accepts that MEPC 107(49) does not specifically require the fitting of flow or pressure
sensors.
Considerations during testing
The following sets out AMSA’s considerations when testing oily water separators during port state control inspection with respect to two types of systems approved under MEPC 107(49):
– MEPC 107(49) approved system that is fitted with an effluent sample flow sensor to 15ppm bilge alarm.
Operational testing of the equipment is performed by stopping the sample water flow to the 15ppm bilge alarm. If the 15ppm bilge alarm does not alarm when effluent sample flow is stopped for more than 5 seconds, and the automatic stopping device is not activated within 20 seconds, this is considered a failure of the oily discharge monitoring and control system and the 15ppm alarm arrangements. The ship is likely to be detained until the system complies with MARPOL requirements.
– MEPC 107(49) approved system that is not fitted with an effluent sample flow sensor to the 15ppm bilge alarm.
The sample water flow through 15ppm bilge alarm should be unobstructed. All valve(s) fitted for sampling line to the 15ppm bilge alarm should be in the normal operating position when testing is performed during port state control inspections.
During the test the following will be considered:
– If operational testing of the equipment commences with effluent sample valves open, this is evidence of the system being used correctly in service. If there is no 15ppm bilge alarm and automatic stopping device activation after shutting the effluent sample valve, then the equipment is non-compliant. The equipment must be made compliant. As a temporary measure, valves to and from 15ppm bilge alarm can be secured and sealed open to ensure the flow of effluent sample cannot be stopped or manipulated whilst the equipment is operating, as required by MEPC 107(49) 4.2.10.1.
– If operational testing of the equipment commences with the effluent sample valve shut or no flow of effluent sample possible through the 15ppm bilge alarm and the automatic stopping device does not activate, this is viewed as evidence that wilful manipulation of the equipment is possible. As pollution of the environment may occur, the ship is likely to be detained until the equipment complies and crew are sufficiently familiar with the operation of the system.
– If operational testing of the equipment commences with the effluent sample valve closed and with clean water, used for cleaning or calibration, flowing through the 15ppm bilge alarm and the automatic stopping device does not activate, then the equipment is non-compliant to MEPC 107(49) 4.2.10.2. The ship may be considered for detention until the equipment complies and crew are sufficiently familiar with the operation.